Robotic simulations are essential tools in the design and development of robotic systems. They allow engineers to test and refine concepts in a virtual environment before deploying them in the real world. Here are examples of simulations that can significantly improve the design and performance of robotic systems:
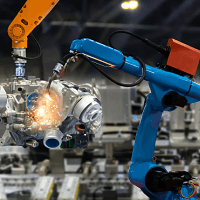
1. Kinematic and Dynamic Simulation for Robotic Arms
Purpose: To test and optimize the movement of robotic arms in various tasks.
Simulation Details: This simulation models the kinematics (motion without considering forces) and dynamics (motion considering forces) of robotic arms. It includes simulations of joint movement, torque application, and interaction with objects.
Outcome: Engineers can optimize the arm’s reach, speed, and force application, ensuring that the robot can perform tasks such as assembly, welding, or painting with precision and efficiency. It also helps in identifying potential issues like joint wear or collisions in complex tasks.
2. Autonomous Navigation and Path Planning Simulation
Purpose: To test the robot’s ability to navigate complex environments autonomously.
Simulation Details: This involves simulating the robot’s sensors (e.g., LIDAR, cameras) and control algorithms as it navigates through an environment filled with obstacles. The simulation tests various path-planning algorithms like A* or Dijkstra’s to determine the most efficient route.
Outcome: Engineers can refine the robot’s ability to avoid obstacles, optimize travel paths, and reduce energy consumption. This is crucial for autonomous vehicles, drones, or mobile robots operating in dynamic environments such as warehouses or urban settings.
3. Sensor Fusion and Localization Simulation
Purpose: To enhance the robot’s ability to accurately perceive its environment and location.
Simulation Details: This simulation integrates data from multiple sensors (e.g., cameras, IMUs, GPS) to improve the robot’s understanding of its surroundings. Simulations can include various conditions like low-light environments, signal interference, or sensor failure.
Outcome: By testing and refining sensor fusion algorithms, engineers can improve the robot’s accuracy in localization and mapping (SLAM), leading to more reliable navigation and task execution in diverse environments.
4. Human-Robot Interaction (HRI) Simulation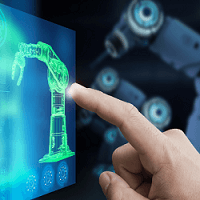
Purpose: To optimize the robot’s interactions with humans, ensuring safety and efficiency.
Simulation Details: This involves simulating scenarios where robots and humans work together, such as collaborative robots (cobots) on an assembly line. The simulation tests various interaction models, such as gesture recognition, voice commands, and safety protocols.
Outcome: Engineers can design robots that better understand and respond to human actions, reducing the risk of accidents and improving the overall efficiency of human-robot collaboration in workplaces.
5. Grasping and Manipulation Simulation
Purpose: To optimize the robot’s ability to grasp and manipulate objects of various shapes and sizes.
Simulation Details: The simulation models the interaction between the robot’s gripper or end-effector and different objects, considering factors like grip force, object weight, and surface texture. It tests various gripping strategies to determine the best approach for different objects.
Outcome: Engineers can design grippers that are more versatile and capable of handling a wider range of objects, improving the robot’s performance in tasks like packaging, sorting, or assembly.
6. Environmental Stress Testing Simulation
Purpose: To evaluate the robot’s performance in extreme conditions.
Simulation Details: This simulation subjects the robot to various environmental stressors, such as high temperatures, corrosive environments, or high vibration. It tests the durability and reliability of components under these conditions.
Outcome: Engineers can identify potential failure points and make design adjustments to ensure the robot can withstand harsh environments, which is critical for applications like space exploration, underwater robotics, or industrial automation.
7. Multi-Robot Coordination Simulation
Purpose: To test the coordination and communication between multiple robots working on a shared task.
Simulation Details: This involves simulating scenarios where multiple robots need to collaborate, such as in a swarm or a factory floor. The simulation tests communication protocols, task allocation, and synchronization strategies.
Outcome: Engineers can refine algorithms that enable robots to work together efficiently, reducing bottlenecks, preventing collisions, and ensuring smooth task execution in collaborative environments.
8. Energy Efficiency and Power Management Simulation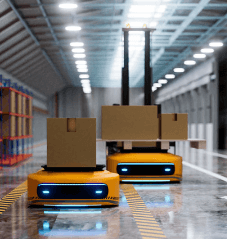
Purpose: To optimize the robot’s energy consumption for extended operation.
Simulation Details: This simulation models the robot’s power usage across different tasks and operational modes. It tests various power management strategies, such as dynamic power scaling or energy harvesting techniques.
Outcome: Engineers can optimize the robot’s power consumption, extending battery life and improving the overall efficiency of operations, which is crucial for mobile robots, drones, and remote or autonomous systems.
9. Failure Mode and Effects Analysis (FMEA) Simulation
Purpose: To identify and mitigate potential failure points in the robotic system.
Simulation Details: This simulation runs the robotic system through a series of stress tests, simulating component failures or software errors. It analyzes the impact of these failures on the overall system performance and identifies critical vulnerabilities.
Outcome: By understanding potential failure modes, engineers can design more robust systems, implement fail-safes, and improve the reliability of the robot, reducing downtime and maintenance costs.
10. Behavioral Simulation for Autonomous Robots
Purpose: To test and optimize the decision-making algorithms of autonomous robots.
Simulation Details: This involves simulating complex environments where the robot must make decisions based on sensor inputs and pre-programmed behaviors. The simulation tests various scenarios, including emergency situations, to ensure the robot’s decision-making process is sound.
Outcome: Engineers can refine the robot’s AI algorithms to make better, faster decisions in real-time, improving the robot’s autonomy and effectiveness in dynamic environments such as disaster response or military operations.
These simulations provide critical insights during the design phase, allowing for the optimization of robotic systems before they are built, ultimately leading to more reliable, efficient, and effective robotic solutions.