Custom and COTS Integration has been a cornerstone of many successful projects, enabling innovative solutions for complex challenges. Here are examples of how this approach is applied:
1. Underwater Robotics 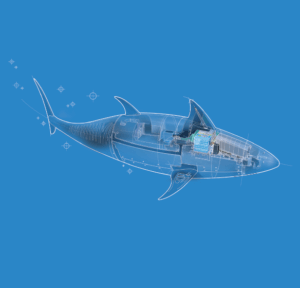
Purpose: To enable reliable operation in deep-sea environments.
Integration Details: Custom pressure-resistant housings are combined with COTS sensors such as sonar and navigation modules. These integrations ensure durability and precise mapping capabilities under extreme pressure conditions.
Outcome: The resulting system provides robust performance for applications like deep-sea exploration, reducing operational risks and delivering high-quality data.
2. Magnetic Crawlers
Purpose: To inspect ferrous surfaces in industrial environments.
Integration Details: Custom magnet arrays are integrated with COTS mobility components, including motors and wheels. This design allows the robot to traverse steel structures such as ship hulls and storage tanks.
Outcome: The crawler navigates hazardous and hard-to-reach areas with efficiency, improving safety and inspection accuracy.
3. Bio-Inspired Vehicles
Purpose: To enhance maneuverability and energy efficiency in underwater applications.
Integration Details: Tailored propulsion mechanisms, inspired by aquatic life, are combined with COTS power units and control boards. This integration optimizes agility and stealth in underwater operations.
Outcome: The vehicle excels in tasks such as environmental monitoring and infrastructure inspection, reducing energy consumption while maintaining precision.
4. Predictive Maintenance Systems 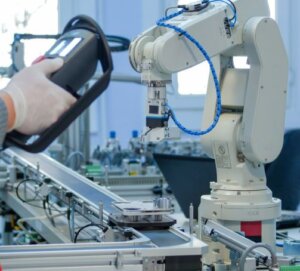
Purpose: To monitor and prevent equipment failures.
Integration Details: Custom diagnostic algorithms are paired with COTS sensors to track the health of components like motors and bearings. These systems predict wear and tear before critical failures occur.
Outcome: Predictive maintenance reduces unexpected downtime and extends the lifespan of robotic systems, offering significant cost savings.
5. Multi-DOF Robotic Arms
Purpose: To perform intricate tasks with precision.
Integration Details: Custom actuators and end-effectors are integrated with COTS motion controllers to enable precise manipulation of small or delicate parts.
Outcome: The robotic arm delivers unmatched accuracy and flexibility in industries like precision manufacturing, meeting exacting standards for quality and efficiency.